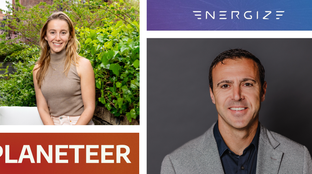
🌎 Two climate investors on raising in today's tough market
Q&As with Sophie Purdom, who just closed first-time Planeteer Fund I, and John Tough, who recently closed Energize Capital's mega-fund Ventures Fund III
If their founding story holds any sign of the future, Molten’s start in a Palo Alto garage means that they’re off to a good start. Molten’s ambitions to decarbonize methane pyrolysis - and the practicalities of 1,400 degrees Celsius temperatures - necessitated a brisk graduation to grander and safer digs. With fresh Seed capital from USV and Fifty Years and a Breakthrough Fellowship locked and loaded, we Zoomed in with Kevin Bush to learn more about Molten’s plans to make reactors that don’t clog, and produce (lots and lots of) clean Hydrogen in the future
What’s Molten’s founding story and how did the team come together?
When the world shut down in March 2020, I went through a small existential crisis. I used to be in the camp of environmentalists that believed in “electrify everything” – that we had to go 100% renewable energy in order to hit net zero. But even when the pandemic slowed the world economy to a crawl, the impact on emissions was relatively small. I became worried that electrification alone would struggle to decarbonize heavy industrial sectors with the urgency required to mitigate climate change.
I reached out to my now co-founder Caleb Boyd, who I did my PhD with at Stanford, and we set up a weekly call to discuss new climate tech ideas. He was working in venture capital in Germany at the time, and I would run every idea that popped in my head past him. We debated compressed air energy storage, electro-chemical direct air capture, giant screws for energy storage, and autonomous balloons to collect methane leaks from taliks in the Arctic permafrost. (I hope someone actually goes and works on the last one!)
But none of this stuck – we kept on getting drawn back to clean hydrogen production.
What was so compelling about clean hydrogen production?
Initially, I didn't know much about hydrogen. I thought of hydrogen as this futuristic fuel that would power our transportation in the future. But hydrogen is a very real, almost $100B market today, used as a chemical feedstock for petrochemical refining and ammonia fertilizer production. We make almost all of this hydrogen with a process called steam methane reforming, which produces about 10 tonnes of CO2 per tonne of hydrogen. When you're making 100 million tonnes of hydrogen a year, that equates to about a billion tonnes of CO2 emissions. This is a big problem.
If you can think of a way to develop clean hydrogen that’s really cost-competitive with steam methane reforming, you can decarbonize all sorts of big industries like cement, steel, and transportation which are responsible for about 25% of global CO2 emissions.
You had a starting thesis on methane pyrolysis. How did you begin to test it out?
During the pandemic, I moved back to a faculty house at Stanford owned by two psychiatry professors. They had this garage that they kindly allowed me to clean out for some experiments. We built the simplest reactor we could in this garage, watching YouTube videos on how to build furnaces that could get up to 1,400 degrees Celsius. Our furnaces basically consisted of wrapping a wire around a ceramic tube and insulating it, which we then hooked up to my landlord’s EV charger. They were incredibly lenient landlords - and made for this true garage startup story.
So what exactly is Molten’s technology?
We are specifically focused on methane pyrolysis, or methane cracking. Methane cracking is where we heat up methane over 1,000 degrees Celsius, and thermally decompose it into solid carbon and hydrogen.
This is not a new concept – people have understood the thermal decomposition of methane for over a century. But no one's been able to make a high-throughput, simple reactor that can operate continuously without clogging. There is a carbon deposition problem inside the reactor, which coats all heating surfaces and eventually clogs the reactor.
To put it simply, Molten makes reactors that don't clog. There are other pathways like plasma routes and microwave heating to crack methane, which still often deal with a carbon buildup problem and are very energy-intensive. On the other side, there are catalytic processes which lower the temperature but still coat all of their catalyst particles with solid carbon. In our reactor, we're directly heating up methane with renewable electricity and resistive heating, and have developed a method to fluidize out all that carbon so it doesn’t clog.
What’s your unique insight that allows you to make these reactors?
Firstly, no one has been super motivated to do this before. A lot of the oil and gas companies looked at methane cracking at the same time they were researching steam methane reforming, but found that steam reforming was an easier problem to solve.
Now that the world is talking about how to create low-cost hydrogen without the CO2 emissions, this technology is being brought back to the forefront. We’re seeing strong demand from a lot of the existing uses of hydrogen, including ammonia production, petrochemical refining, and reducing iron. Large steel producers are looking to replace their existing coal-powered blast furnaces with hydrogen-based direct reduced iron furnaces. Our technology is very amenable because hydrogen comes out of our reactor at 1,200 degrees Celsius and can immediately go into a direct reduction furnace to reduce iron ore to iron.
All of these industries need to operate reactors continuously using steam methane reforming, so there is a lot of interest in introducing methane pyrolysis as a carbon-neutral, or even potentially carbon-negative, process.
Explain methane pyrolysis. Why methane pyrolysis versus electrolysis?
Electrolysis is the main way people think about producing low-carbon hydrogen, and we did look at it. But water electrolysis relies on electricity that costs one to two cents per kilowatt-hour to be cost-competitive. Only wind and solar can achieve that cost of renewable electricity, which are inherently intermittent resources. But these big chemical processes require a continuous supply of hydrogen, and solving intermittency with storage and transportation adds a lot of cost to hydrogen. As a result, we had a hard time betting on the chance that electrolysis could compete with steam methane reforming on a cost basis, which was the impetus to move toward pyrolysis.
The other thing is urgency. Over the past 20 years, we’ve probably invested a trillion dollars into natural gas infrastructure. Our technology can leverage that infrastructure, and that speed can help us avoid several tipping points that could lead to two or three degrees Celsius of warming.
What does the competitive landscape look like in the green hydrogen production space?
We plan to be twice as energy-efficient as other methane pyrolysis companies, and we also don’t have to deal with the carbon contamination problems that most of the catalytic pyrolysis companies deal with. We also require significantly less electricity than electrolysis, which lowers costs.
What are the KPIs or key milestones you’re looking to hit? What have you achieved so far?
We are currently running a reactor that we built with just a few thousand dollars that can process one kilogram per day – a similar throughput to companies that have raised tens of millions of dollars. We just moved to an old steel building in Oakland, where we’re working on building a 50 kilogram per day system, capable of expanding to up to 200 kilograms per day. From there, we want to scale up again to about one tonne per day, which is about equivalent to what a hydrogen refueling station in California typically uses.
Our Oakland facility can scale up to about one tonne of hydrogen per day, which can get us to demonstration scale. From there, we need to scale up to 10 tonnes per day to be able to address large chemical plants. But once we get to one tonne per day, we hope we can scale by just copy-pasting, or modularizing, the reactor.
What markets does Molten plan to plug into? How?
We’re targeting the fertilizer and chemicals markets first which already have an existing, massive demand for hydrogen. We plan to be a producer, which will require partnerships to be able to develop methanol, ammonia, etc.
We’re looking to form offtake agreements with these chemical plants for hydrogen production. Offtake agreements are akin to a power purchase agreement for electricity – you promise that you’ll produce some amount of hydrogen, and the partner agrees to purchase that hydrogen from your facility.
Hydrogen production seems to be going down the path of solar, where it becomes a race on cost and scale. How will you beat electrolyzers manufactured at-scale?
I hope we can scale up electrolyzers and decrease the costs for green hydrogen, similar to how China reduced the cost of silicon solar cells down to prices where it made sense to install solar farms over coal plants. But the compression, storage, and distribution required for water electrolysis is a challenge, given we don’t have large-scale hydrogen pipeline infrastructure in the US. We plan to integrate into chemical plants or iron reduction furnaces in the same way steam methane reforming is currently integrated where hydrogen is consumed at the point of production and there is little or no on-site storage.
What we're building with methane pyrolysis uses five times less renewable electricity than water electrolysis, which enables us to afford five times higher electricity prices. This is important because it opens up a broader spectrum of potential renewable electricity sources in the 5 to 7 cent per kilowatt-hour range, such as hydro-electric, geothermal, nuclear, or wind and solar plus storage.
Walk through the unit economics and key assumptions. Â Is this an opex or capex cost reduction? Â
Most chemical plants have 20 to 30 year lifetimes, so the capex is a fairly small portion of our overall cost. The two main factors of our cost are the feedstock of either natural gas or biomethane, and renewable electricity. But we can achieve hydrogen prices of less than $1.50 per kilogram with electricity costs of about five cents per kilowatt-hour, which you can find today in places like Texas, Oklahoma, and Washington.
Methane pyrolysis still requires natural gas. What’s your take on the relative emission impact versus electrolysis?
Our process is carbon-neutral, and if we use biomethane, it would actually be carbon-negative. If we use natural gas, we do have to worry about our upstream supply chain emissions and leakage. We're working with companies like Project Canary to monitor and limit methane emissions, and it’s also exciting that there’s a lot of funding in the Inflation Reduction Act to support this.
Congrats! You recently announced your seed round and participation in Breakthrough Fellows. Who’s involved and what’s next?
We're really excited to have support from USV and Fifty Years, as well as funding from UVC Partners (where Caleb used to work) and J4 Ventures, and Moai Capital. We’ve also received support from Breakthrough Energy as part of the Fellows program. We're excited to grow the team, and we're hiring mechanical and chemical engineers to help prove out the operational stability of our reactor at scale.
Molten has graduated from their backyard garage into a 10,000 sq ft facility in Oakland, CA, and is scaling the team to boot! Check out their open engineering roles, and reach out to chat if you’re deploying methane pyrolysis or replacing steam methane reforming. Massive thanks to Claire Yun who cracked this story!
Q&As with Sophie Purdom, who just closed first-time Planeteer Fund I, and John Tough, who recently closed Energize Capital's mega-fund Ventures Fund III
A Q&A with Precursor's David Yeh and Mark1's Julian Ryba-White, new strategic partners in the ecosystem
A Q&A with the DOE LPO director Jigar Shah and Solugen CEO Gaurab Chakrabarti