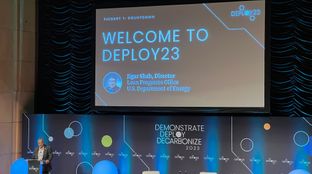
đ Demonstrate, deploy, decarbonize with DOE
âGovernment-enabled, private sector-ledâ in action in Washington, DC
What does clinker have to do with $20m of prize money?
A 5 year global competition. 100 starting teams. -20°F working conditions in Alberta. $20,000,000 prize pool. 2 winners. And 8% of global greenhouse gas emissions on the line.
The NRG COSIA Carbon XPRIZE just anointed the winners of its five-year global competition to develop breakthrough technologies that convert the most CO2 into products with the highest net value: CarbonBuilt and CarbonCure. Whereas past early media darlings of the carbon to value movement use CO2 as an input into soda, vodka, or diamonds, the XPRIZE grand winners leapfrogged niche use cases and coincidentally both address a building block (literally) of carbon emissions - cement and concrete production.
The happy winning companies return home with $7.5m in their pockets, a working at-scale prototype, and global media coverage. More from the CEOs of CarbonBuilt and CarbonCure below - but first a primer on the cement and concrete industry. Laying the foundation for our understanding, we spoke with Eric Trusiewicz, a fellow at Stanford University and former international cement executive.
For the next 40 years, global development is expected to expand at the rate of adding a New York City-sized construction footprint every month - or 2T sq ft of buildings by 2060. A majority of this physical footprint will be concrete, whether in the form of bridges, roads, walls, and sewer systems. Globally, ~25b tonnes of concrete are produced each year - an incomprehensible amount, with the 8% of global emissions footprint to match.
To understand concreteâs raw material and emissions scale, letâs go back to the start (of the factory line). Concrete is a mix of crushed stone and sand glued together with cement (the binder). After being quarried and crushed, raw limestone and clay inputs are mixed and heated up in a rotating kiln. At the high temperature of 1450°C, limestone (calcium carbonate) is converted to lime (calcium oxide), releasing CO2 during the calcination process. Calcination itself naturally produces more than half of cementâs CO2 emissions. The bulk of the remaining emissions come from the thermal energy (generally fossil fuel) needed to heat the kiln. The resulting âclinkerâ material is then ground with gypsum and other supplementary cementitious materials (aka SCMs - more on this later!) to produce cement.
At this point, the supply chain diverges into on-site and off-site production paths. ~80% of global cement supply is used on-site (think: âbeware wet cement!â signs at worksites) where cement gets mixed with sand, water, and gravel. The remaining ~20% of global cement is âprecastâ into building components like masonry blocks off-site at factories.
Cement production far outpaces the growth of the global population (by ~11x since 1950) with 90% of consumption now in the developing world. Meanwhile, the cash cost of production remains dirt cheap at $20-40 / tonne. Multinational players control the market with $1T of invested capital stock, enormous limestone reserves, and an aggressive attitude towards competition. But one thing that these formidable competitors (or potential allies) can get behind: variable cost reduction. As Eric foreshadows, âCement companies tend to be keen to support technology development thatâs cost effective, and CO2 emissions cost is an increasing reality for them. Startups run by teams which pair technological innovation with realistic  understanding of the dynamics of the industry can bring enormous benefits to the sector.â
Curious for more? Check out Ericâs incredible primer on the cement industry and decarbonization pathways.
We congratulated and chatted with the leadership of CarbonCure, President Jennifer Wagner, and CarbonBuilt, CEO Rahul Shendure, both of whom were quick to credit their respective teams for the 5 years of hard work that went into winning the XPRIZE. Jennifer and Rahul share their perspectives on the journey, scope of the cement emissions problem, and what comes next for their companies.
CarbonCure [Jennifer Wagner, President]: I actually wasn't surprised that both winners provide concrete solutions. The concrete industry represents the largest opportunity to consume CO2, given the massive volume of concrete that we're producing every year and decades of coming construction demand.
The carbon utilization industry is expected to create $1T+ of new market opportunities and could reduce global emissions by up to 15% by the end of this decade. When you look at all of the things that you can make from CO2, concrete represents by far the largest opportunity and offers a permanent carbon storage pathway. Making other products from CO2 like fuel offers a temporary form of storage. Fuel made with waste carbon will eventually get burned and the CO2 molecule will end up back in the atmosphere, whereas the CO2 we inject into concrete is permanently embedded.
CarbonCure was established about a decade ago to respond to the two key growth trends of construction and decarbonization. Concrete is the most abundant man made material and represents ~8% of global emissions. We've shown that concrete can be part of the solution to fight climate change by developing a solution to consume and mineralize waste carbon dioxide within concrete.
CarbonBuilt [Rahul Shendure, CEO]: On an annual basis, cement production is responsible for about almost 10% of global emissions. Roughly 60% comes from the fundamental chemistry of the calcination process and the other 40% comes from the coal used for energy to drive the process. No oneâs developed an economically viable and scalable alternative that can make a dramatic change in that profile, and carbon capture and storage (CCS) isnât economically feasible at present. So that's where utilization of CO2 in concrete comes in.
In theory, you can do many different things with CO2. In prioritizing these, the criteria that ought to matter most are economic viability and scale potential, and there are only a few applications that have the scale to make a meaningful impact. Concrete, aggregates, and fuels are the only things that could deliver a gigaton of annual reductions. Beyond scale, the economics need to be compelling enough for incumbents to make a leap in adopting new technology. The economic and technical risks for utilization in fuels and aggregates are much higher than for utilization in concrete, and significant investment will be required to try and get down the cost curve. Two concrete startups winning the XPRIZE is, I think, indicative of concreteâs much clearer path to large-scale near-term impact than other utilization options.
CarbonCure: We offer a solution for concrete producers to recycle waste carbon dioxide to make concrete. Our technology injects CO2 during the concrete mixing process, which spurs a chemical reaction that permanently mineralizes CO2 within the concrete. What's interesting is that the addition of CO2 also makes the concrete stronger, which enables the concrete producer to use less cement and unlocks further decarbonization and economic benefits. Our concrete allows the producer to differentiate their products in the market, generating a business case for adoption as well.
Our mission is to reduce 500m tonnes of CO2 annually by 2030. We've been quite transparent on how we're planning to achieve that target through two avenues: 1) geographic expansion and 2) continued innovation. Right now, nearly 350 concrete plants around the world use our technology, and we have plans to accelerate that ramp to new international markets. On the second pillar, weâve been developing new technologies that recycle CO2 and concrete - one of which was demonstrated as part of the Carbon XPRIZE - a solution for concrete reclaimed water which treats waste water generated at a concrete plant with CO2. We're also working on a solution to carbonate recycled aggregate, which would allow for waste concrete to be recycled back into the production process. And we're leveraging digital solutions to create additional production efficiencies and drive down emissions even further.
CarbonBuilt: Our process, which is implemented in the factories where masonry and precast concrete products are produced, involves changes to both concreteâs formulation and its curing process.
On the materials side, we add portlandite, which is an existing commodity chemical made from limestone at a temperature thatâs about 600°C lower than that required to produce Ordinary Portland Cement (OPC). It's priced about the same as cement and has a slightly better carbon footprint. Using portlandite allows us to cut cement content by 60-90% and increase the use of low cost, low carbon materials such as fly ash or slag.
On the process side, we're uniquely able to cure concrete with dilute CO2 sourced directly from flue gas, without any capture, purification or pressurization. The economics of other low carbon approaches fall apart when you need materials that arenât widely available and cure concrete with concentrated CO2 delivered at high pressures and temperatures. Concrete is a commodity, after all, so capital intensive processes with high operating expenses wonât be adopted.
When you put these innovations together, you end up with substantial changes to the cost structure of concrete without really changing the supply chain. We enable a 15-20% reduction in the raw materials cost, which alone can expand operating margins by more than 50%. On top of that, weâre embedding substantial amounts of CO2 into the concrete through curing. We can deliver 50-80% reduction in embodied carbon - about 30% of which comes from utilization and the rest from cement reduction - with todayâs technology, while at the same time increasing the profit margin of our customers. Thatâs how you enable gigaton-scale impact.
CarbonCure: What makes us unique is the scalability of our solution since we're leveraging existing infrastructure. There are roughly 100,000 concrete plants on Earth and we can work with all of them. Our technology gets bolted on as a retrofit to existing plants and takes one day to install. After that, they can start supplying low carbon concrete to the market.
What's also interesting is our business model - we don't actually charge any upfront capital to install the equipment. We install it for free, and then the concrete producer pays us a monthly subscription fee. This subscription model reduces the barriers to adoption so we can scale much faster. Our technology also works with every type of  concrete, where some other players in the space are limited to only a segment of the overall concrete market, like blocks or precast.
CarbonBuilt: Concrete is a commodity, and weâre enabling concrete products that perform just like todayâs products. Our value proposition is that we can deliver tangible economic value to producers in the form of raw material cost reductions and monetization of the carbon avoidance and utilization. The best way to drive adoption is by making a substantial improvement in the cost structure for a producer.
I originally approached the UCLA team that developed the technology behind CarbonBuilt as an investor because it struck me that no one had cracked the code yet in terms of substantial decarbonization of concrete. That's the real difference in our approach - the ability to significantly reduce carbon emissions in a way that adds material economic value to the producer.
CarbonCure: The cement and concrete industry is a very well established industry, not much has changed over the last 100 years. Our position has always been to tie into the existing supply chains, and not to disrupt their operations. When you look up and down the value chain, there's a role that every player has in this decarbonization transition. You've seen all the net zero commitments by governments and corporations, and concrete is a key solution to meet some of these commitments. To accelerate the decarbonization of concrete, we can pull  on three different levers across the value chain. The first is carbon offsets. Corporate buyers like Stripe and Shopify understand that we need to invest in climate tech solutions. We actually share our offset revenues from corporates with the concrete producers as an incentive to adopt our technology and drive down their CO2 as quickly as possible.
The folks who are actually building with concrete also play a key role in the low carbon transitioning. If a company like Amazon decides to prioritize low-carbon building materials for their new HQ, they would select our customersâ lower carbon concrete over a less green alternative. The third vector is around government procurement. There are some great examples in the US of state and city legislation requiring or supporting the use of low carbon concrete, which can dramatically help to accelerate adoption of low carbon solutions. These three accelerators - carbon offsets, private sector specifications, and government procurement - can dramatically accelerate adoption.
We've been in business for a decade and our business model now is quite different from 10 years ago. Because we donât charge an upfront fee, a new customer can easily adopt our technology in a couple of plants to see it working in their environment. Once they see the value proposition, they can quickly roll it out across their fleet of plants.
CarbonBuilt: Weâre pre-commercial, so are still testing out our model. Based on what weâve heard so far from concrete producers, our plan is to co-invest with them to retrofit their plants and share in the operating margin gains that result. We're talking about $1M, plus or minus, in total capex to convert a concrete block line. This is very different from a licensing model. It demonstrates upfront to our partners that we believe in the technology and value proposition.
On carbon monetization, weâll take the lead on finding the optimal buyers. Itâs a very different world today than it was a few years ago, both in terms of carbon verification and accounting, as well as corporate demand coming from the likes of Stripe and Microsoft. Our carbon reduction is split into two buckets: 1) carbon avoidance driven by cement reduction and 2) carbon utilization from uptaking and permanently sequestering the CO2, which buyers are willing to pay more for. One thing thatâs great about concrete is that it is an unambiguously permanent sink for CO2.
CarbonCure: We're CO2 agnostic, which means that our technology can use CO2 from any source, so we don't typically get involved in the sourcing side. As long as we've got a tank of CO2 that's being piped in, our system works. Our customers are the ones who pay for the CO2. We have some preferred relationships where we make recommendations for customers to engage, but from a climate perspective it doesn't matter to us where the CO2 comes from.
To protect against any potential supply shortages that may occur in the future, we're looking at alternative CO2 supply opportunities to source CO2 that isnât food grade, which is what most of our customers use today. Direct air capture will also be critical in meeting our long-term climate targets. When that comes online, our system could easily swap out industrially sourced CO2 for DAC.
CarbonBuilt: Sourcing CO2 can be a challenge, but there are lots of concrete producers located very close to sufficiently large CO2 sources, and thatâs where we will start. We have some work to do connecting the dots. In emerging markets, weâll be focused on integration into plants yet to be built. Â With our technology, siting a new plant near a CO2 source can make a significant difference in their economics.
Down the road, weâll be looking at direct air capture as a CO2 source. Our process allows for a different set of specs for DAC that should make it easier for some approaches to hit target costs. Furthermore, because of our economics, we can enable DAC to get to market faster.
CarbonCure: It was a journey to say the least. Our team worked incredibly hard over the five year period and the competition really forced us to push the envelope on what was possible. Physically working in Alberta during -20°F winters was tough on the team, and due to COVID restricting people onsite, we were working with a bit of a skeleton crew. But the team pushed through and obviously the efforts paid off.
We have a portfolio of technologies that all recycle CO2 into concrete, but in slightly different ways. We have technology for concrete masonry (concrete blocks), precast concrete, and ready mix concrete (poured concrete). The technology demonstrated as part of the XPRIZE was our latest innovation, recycling carbon dioxide in concrete reclaimed water. We can collect the wastewater off a concrete plant, treat it with CO2, and recycle both the water and solids (which is primarily cement) back into the concrete production process. So this not only has significant CO2 benefits but also freshwater and solid waste benefits. This technology is now commercially available and operating in our first installation in British Columbia.
All this really ties back to our 500 megaton mission. We'll be leveraging the XPRIZE funds to scale up, continue R&D, and accelerate our pace of growth. Another thing we're trying is dedicating a portion of the funds for social equity causes since climate and social inequity are very much linked.
CarbonBuilt: Our technology was still very early when this project started, and XPRIZE provided a framework and rhythm to drive action and urgency. For the finals last year, we were able to demonstrate the process at a relevant scale, producing full size products that are being used in projects today. One of the reasons we won, I think, is the product volume we were able to make in the context of the demonstration requirements. We've got a 10-15x scale up necessary from demonstration to commercial scale, but itâs all execution risk, not technical. XPRIZE has taken us from being just past first experiments to being on the cusp of commercialization.
UCLA, not CarbonBuilt, will receive the XPRIZE funds. Weâre excited to see what comes out of that work.
Both companies are growing quickly and hiring! If youâre cemented on decarbonizing the concrete industry (hah!), keep an eye on the CarbonBuilt website as they ramp up for their Series A and the CarbonCure careers pages. Likewise, these companies will be built on partnerships and are eager to connect with concrete producers, construction firms, and legislative players.
Feel free to send us new ideas, recent fundings, or general curiosities. Have a great week ahead!
âGovernment-enabled, private sector-ledâ in action in Washington, DC
Well-to-wake pathways to cleaner shipping
Scaling âsymbiotic manufacturingâ with Rubi Laboratories